Now this is a daunting job!!
The front end of Icetiva, a Festi with a B6T I ice race, folded up 'rite nicely on its second weekend of racing. Two cars spun in front of me on two occassions and that was the end of the driver's side frame rail, from just forward of the strut tower. The car has sat for two years now, and it is finally getting some drastic repairs. I never could get a good shot showing the magnitude of the damage, but the rails were too bent to ever make them pretty and straight again. in fact, I could not get angles on them to unfold them at all using hammers and pull chains. A frame shop wanted 14 hours on the frame machine to straighten it.
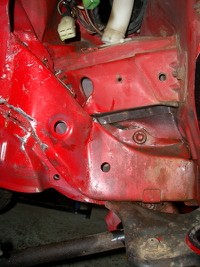
Drastic surgery was suggested, so I went to Pic and Pull and chopped off a front end, then thawed off the snow in our foyer. My wife was pleased with the new decorations, of course. And then I set to work with Hiroki's able help. We guessed at the fit, cut the new piece a little over sized, then took the big step and cut the frame and shell on the car. Then we fine tuned the fit, trimming and grinding as needed. That was several days work.
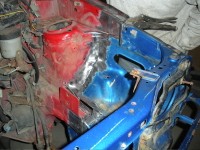
We measured the height above the ground on both sides (compensating for the jack stand height difference), the distance from front rail to trailing control arm mount bracket, the width of the front rail compared to other cars, and the diagonal across the engine bay from the two trailing control arm brackets. A few mounting holes and stamped metal holes were used to double check the position. The new part seemed a touch higher than it should be, but good in all other dimensions. We could not get the height identical on both sides and still retain all the other geometries. Spacers on the sway bar mount brackets will fix the height difference if we need to.
Hiroki then set to work with his excellent welding skills, and started tacking it together. He did a fair amount of reading on how to weld the tissue paper they used for sheet metal on these cars, to avoid burn through. It is now tacked in place. Next he starts on the serious welding, fish plating and strengthening! That will be a few more days work yet.
The front end of Icetiva, a Festi with a B6T I ice race, folded up 'rite nicely on its second weekend of racing. Two cars spun in front of me on two occassions and that was the end of the driver's side frame rail, from just forward of the strut tower. The car has sat for two years now, and it is finally getting some drastic repairs. I never could get a good shot showing the magnitude of the damage, but the rails were too bent to ever make them pretty and straight again. in fact, I could not get angles on them to unfold them at all using hammers and pull chains. A frame shop wanted 14 hours on the frame machine to straighten it.
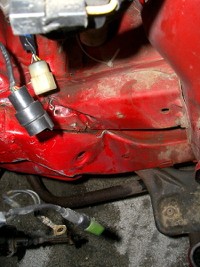
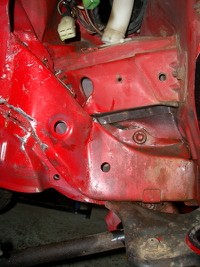
Drastic surgery was suggested, so I went to Pic and Pull and chopped off a front end, then thawed off the snow in our foyer. My wife was pleased with the new decorations, of course. And then I set to work with Hiroki's able help. We guessed at the fit, cut the new piece a little over sized, then took the big step and cut the frame and shell on the car. Then we fine tuned the fit, trimming and grinding as needed. That was several days work.
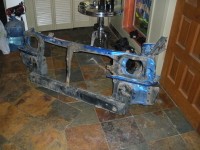
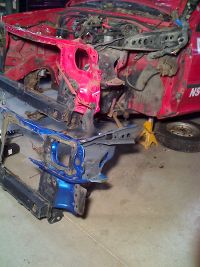
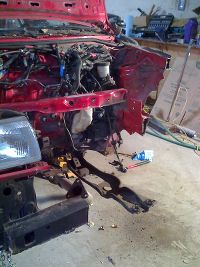
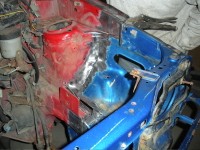
We measured the height above the ground on both sides (compensating for the jack stand height difference), the distance from front rail to trailing control arm mount bracket, the width of the front rail compared to other cars, and the diagonal across the engine bay from the two trailing control arm brackets. A few mounting holes and stamped metal holes were used to double check the position. The new part seemed a touch higher than it should be, but good in all other dimensions. We could not get the height identical on both sides and still retain all the other geometries. Spacers on the sway bar mount brackets will fix the height difference if we need to.
Hiroki then set to work with his excellent welding skills, and started tacking it together. He did a fair amount of reading on how to weld the tissue paper they used for sheet metal on these cars, to avoid burn through. It is now tacked in place. Next he starts on the serious welding, fish plating and strengthening! That will be a few more days work yet.
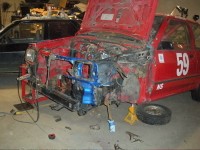
Comment